L'industrie du futur résulte d'une numérisation des outils de production avec toujours plus de capteurs et de données. Les séries temporelles ouvrent de nouveaux horizons tant pour les métiers que pour le développement de nouveaux services.
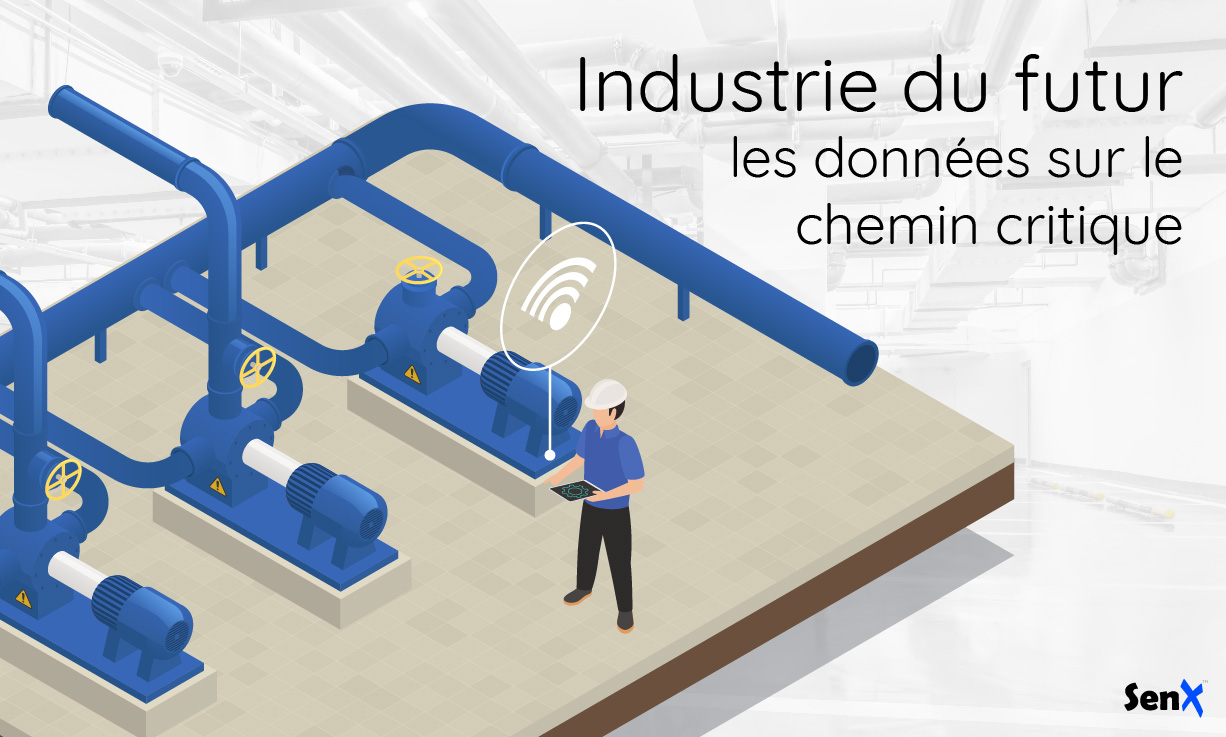
La transformation de l’industrie, sous l’impulsion des technologies numériques, oblige à repenser une chaîne de valeur qui devient techniquement plus complexe. Au-delà du processus de manufacturing, elle modifie en profondeur les relations avec les clients comme avec les fournisseurs. Elle met aussi en lumière le rôle crucial des données à la croisée des enjeux qui associent notamment productivité, qualité, maîtrise des coûts, développement de nouveaux services et concurrence.
Cette évolution s’appuie sur l’intégration de capteurs et de mesures à tous niveaux. Elle a pour conséquence de mettre l’accent sur ce que le traitement des données ainsi générées implique en termes de rupture.
Le présent papier s’inscrit dans une série d’articles sur la manière dont les séries temporelles revisitent le mode d’organisation des données et les technologies utilisées pour leur analyse. Après un premier article de portée générale, les suivants abordent différents secteurs dont le secteur de l’industrie. |
Prefer to read this article in English? It's right here.
Les capteurs ont toujours occupé une place particulière dans l’industrie. Les mesures – avec ses afficheurs – de tension ou de consommation d’électricité, de pression et de température font partie intégrante de l’univers industriel. Au fil du temps, les mesures se sont concentrées vers des postes de supervision de la production ou de l’exploitation. Aujourd’hui, les capteurs ne se limitent plus à effectuer de simples mesures de quelques variables. Ils témoignent d’une numérisation progressive et continue des machines, des systèmes et des processus techniques.
Le secteur de l’industrie sort à peine d’une longue période marquée par une informatisation parfois lourde avec la généralisation des ERP. La généralisation des capteurs ouvre de son côté la voie à une transformation vers l’Industrie du futur. Plus connue à l’échelle internationale sous la terminologie « Industrie 4.0 », elle a comme fil conducteur la donnée qui occupe une valeur désormais stratégique.
Plusieurs écueils peuvent rendre ce parcours difficile.
L’industrie du futur : un enjeu de compétitivité internationale
Le concept le « l’Industrie 4.0 » a été impulsé par l’Allemagne dès 2011. D’abord limitée à la production industrielle, il couvrait principalement le périmètre de l’usine du futur. Aujourd’hui, il englobe généralement tout ce qui relève de la transformation de l’industrie grâce à l’apport des technologies numériques.
Pour les industriels, les enjeux dépassent une simple évolution technique ou technologique de leur outil de production.
Ils conjuguent deux formes de tendances qui sont historiquement contradictoires dans l’industrie. D’un côté la quête d’une diminution des aléas de production, qu’ils soient dus à des ruptures dans l’approvisionnement ou dans la chaîne logistique, ou qu’ils résultent d’une indisponibilité des moyens de production. De l’autre, une pression concurrentielle vers des produits toujours plus personnalisés pour des clients plus exigeants en de services le tout dans un contexte qui impose des règles plus contraignantes en termes d’énergie, d’environnement, de sécurité …
Les piliers de l'industrie du futur
Le Boston Consulting Group a formalisé en 2015, 9 piliers qui caractérisent le passage à l’industrie du futur. Largement reprise, cette représentation met notamment au premier plan le rôle majeur du traitement et de l’analyse des données. Deux autres piliers y sont directement liés : l’Internet Industriel des Objets (IIoT) et la simulation avec le jumeau numérique (Digital Twin). On pourrait également y ajouter le pilier « Intégration horizontale et verticale des systèmes » qui met en évidence la nécessité de disposer d’une organisation technique des données permettant une telle intégration.
Les capteurs – le pilier IIoT – jouent le rôle de catalyseur dans cette évolution. Leur développement conditionne la manière dont les industriels vont répondre à la double contrainte exposée ci-avant :
- Diminuer les aléas : les machines et les systèmes sont de plus en plus complexes avec une forte pénétration de l’électronique et des logiciels techniques qui tendent à optimiser le fonctionnement global comme celui de chaque composant en s’appuyant sur des mesures de capteurs en continu. À l’instar d’une voiture truffée d’électronique, la maîtrise mécanique ne suffit plus. Les capteurs permettent, par eux-mêmes, de répondre aux exigences du renforcement de la qualité de fonctionnement tout en permettant de mieux détecter les anomalies. Les utilisateurs internes tout comme les clients entendent mieux contrôler et éviter de subir les aléas du fonctionnement des systèmes complexes.
- Répondre aux enjeux de la personnalisation dans un contexte concurrentiel et réglementaire plus contraint. Tout se mesure, à la fois pour articuler correctement les interdépendances des systèmes, pour monitorer tout ce qui peut l’être et pour alléger, autant que possible, la charge et la pression sur les hommes.
La plupart des autres piliers de l’Industrie 4.0 peuvent se concevoir comme des composants qui pourront être ajoutés progressivement. Mais celui plus complexe de l’intégration horizontale et verticale des systèmes reste une épine technologique et organisationnelle en matière de transformation.
L'industrie du futur résulte d'une numérisation des outils de production avec toujours plus de capteurs et de données. Les séries temporelles ouvrent de nouveaux horizons pour les métiers & le développement de nouveaux services. Share on XAu moins deux raisons peuvent être avancées :
- Les systèmes reposent à différents niveaux sur une notion de responsabilité fonctionnelle et organisationnelle qui se traduit par des systèmes d’information en silos. Les architectures intégrées peuvent être séduisantes sur le principe, mais délicates à mettre en œuvre d’un point de vue technique et complexes sur un plan organisationnel avec son pendant financier (qui paye quoi ?).
- Cette verticalité en silos implique de fortes contraintes techniques sur l’organisation des données. Alors qu’il faudrait pouvoir facilement croiser les différentes sources de données, ce travail se révèle, au contraire, fastidieux et techniquement difficile du fait de l’hétérogénéité du format et du sens réel de chaque source de données.
Dans l’industrie, ces contraintes sont d’autant plus marquées que le périmètre du numérique couvre deux ensembles encore trop éloignés : les systèmes d’information de l’entreprise (ou informatique de gestion) d’une part, et l’informatique technique, d’autre part.
Découvrez comment les données de séries temporelles permettent de créer des jumeaux numériques d'actifs et jouent un rôle majeur dans l'utilisation de l'IA dans l'industrie du futur. Lire l'article (en anglais) |
La séparation entre l’informatique de gestion et l’informatique technique
La nécessité de disposer d’une vision globale opérationnelle et financière, et la recherche constante d’optimisation des processus a conduit à une généralisation des ERP, qui, plus encore que dans d’autres secteurs, se sont progressivement imposés dans la plupart des entreprises industrielles. Avec des modules dédiés, les ERP couvrent notamment l’approvisionnement, la gestion des actifs, la gestion de la production, la gestion de la maintenance, la vente, la comptabilité et les ressources humaines. Les ERP couvrent ainsi l’ensemble de l’informatique de gestion (ou IT / Information Technology).
Du côté des machines et des systèmes techniques qu’il faut produire et qu’il faut ensuite opérer, on bascule dans un autre univers : celui de l’informatique industrielle ou OT (Operation Technology). Le contrôle et la commande des machines et systèmes nécessitent des dispositifs spécifiques pour s’adapter à des champs de contraintes très variés.
Dans l’exemple d’une usine, l’ensemble de la chaîne est plus complexe. Elle peut être représentée comme suit :
Le SCADA
Plus globalement, qu’il s’agisse de l’usine elle-même ou machines ou systèmes en production, le lien entre le monde des systèmes informatiques (IT) et l’univers des machines et systèmes techniques (OT/Operational Technologies) se fait au niveau des SCADA (Supervisory Control and Data Acquisition). C’est la pièce centrale qui permet de contrôler un ou plusieurs systèmes, machines ou dispositifs techniques à partir des informations remontées par ces derniers, des ordres et commandes qu’il peut recevoir d’autres applications ou d’opérateurs métiers qui, pour cela, disposent d’une interface homme-machine (IHM).
Associé au SCADA, il existe de plus en plus fréquemment un Data Historian qui va enregistrer les flux de données locales. Des outils d'analyse peuvent être associés aux Data Historians. Ils vont notamment permettre de répondre à des questions basiques sur les statistiques de fonctionnement des machines, des systèmes ou de tout dispositif équipé d’un capteur, comme une vanne, par exemple. Ceux-ci peuvent être également rapatriés, totalement ou partiellement, à un niveau central.
Le SCADA peut contrôler plusieurs machines et systèmes. Selon les cas, le lien peut être direct ou s’effectuer avec chacun d’entre eux via d’autres dispositifs décentralisés (identifiés sur le schéma précédent sous les appellations de PLC, DCS ou RTU). Dans un certain nombre de cas, ces dispositifs sont directement intégrés à la machine ou système pour son pilotage opérationnel et son contrôle.
On peut faire l’analogie sur cet empilement de systèmes avec le contrôle d’un téléviseur. La box fait le lien avec l’opérateur et contrôle la télévision. Celle-ci est elle-même équipée de son propre système d’exploitation. L’utilisateur dispose d’un interface pour accéder au service de la box et d’un autre pour accéder à la télévision. Il peut y avoir recouvrement de plusieurs fonctions entre les services proposés par la box et par la télévision. |
Le lien entre les SCADAs qui contrôlent les systèmes techniques et l’informatique est rarement direct. En général, il s’effectue via des logiciels de gestion de la production, de ses processus, de son ordonnancement et du pilotage opérationnel de l’ensemble. Dans le cas d'une usine, le MES (Manufacturing Execution System) occupe une place particulière dans l’ordonnancement des tâches et l’organisation globale des chaînes de production.
Autant dire que les moyens informatiques d’un acteur industriel organisé autour de son ERP et l’univers des machines avec leurs systèmes de contrôle et leurs automatismes ont toutes les raisons d’être bien éloignés l’un de l’autre.
Pourtant, l’intégration des univers de l’IT et de l’OT est incontournable. Deux exigences l’impose dans un contexte industriel toujours plus concurrentiel : la nécessité de toujours mieux répondre aux contraintes opérationnelles, d’une part et la transformation des services aux clients, d’autre part.
Les usages
Le prochain article portera sur les deux usages principaux des données de capteurs dans l’industrie. Un premier usage qui est le prolongement naturel de la raison d’être des capteurs dans l’industrie, à savoir l’optimisation du fonctionnement des systèmes. Le second est plus nouveau et porteur de possibles bouleversements pour les entreprises : le développement de nouveaux services à destination des clients.
Suivez SenX et Warp 10 sur Twitter pour ne pas manquer les prochains articles du blog.
La suite dans la 2e partie.
Découvrez les différentes étapes de maturité de l'industrie du futur dans la vidéo ci-dessous.
Read more
Edge computing: Build your own IoT Platform
Thrift and Protocol Buffers support in WarpScript
Bite the Bytes, WarpScript bitwise operators review
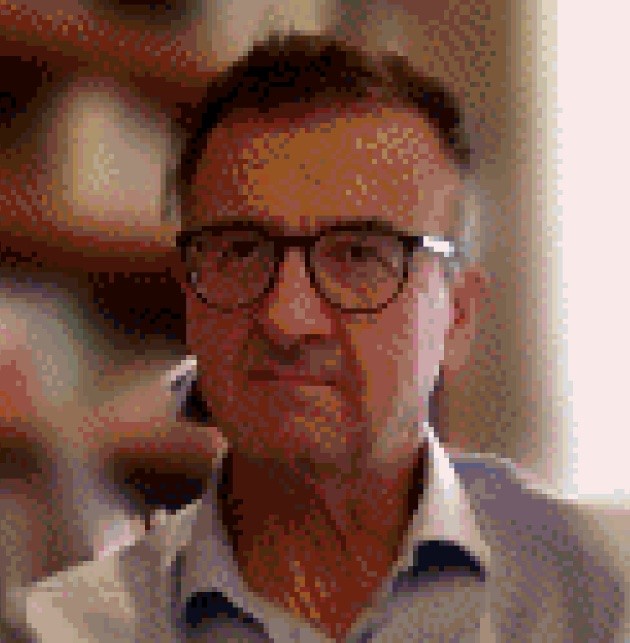
Co-Founder & former CEO of SenX