Industry 4.0 results of the digitization of production tools with ever more sensors and data. Time series opens up new horizons both for business lines and for the development of new services.
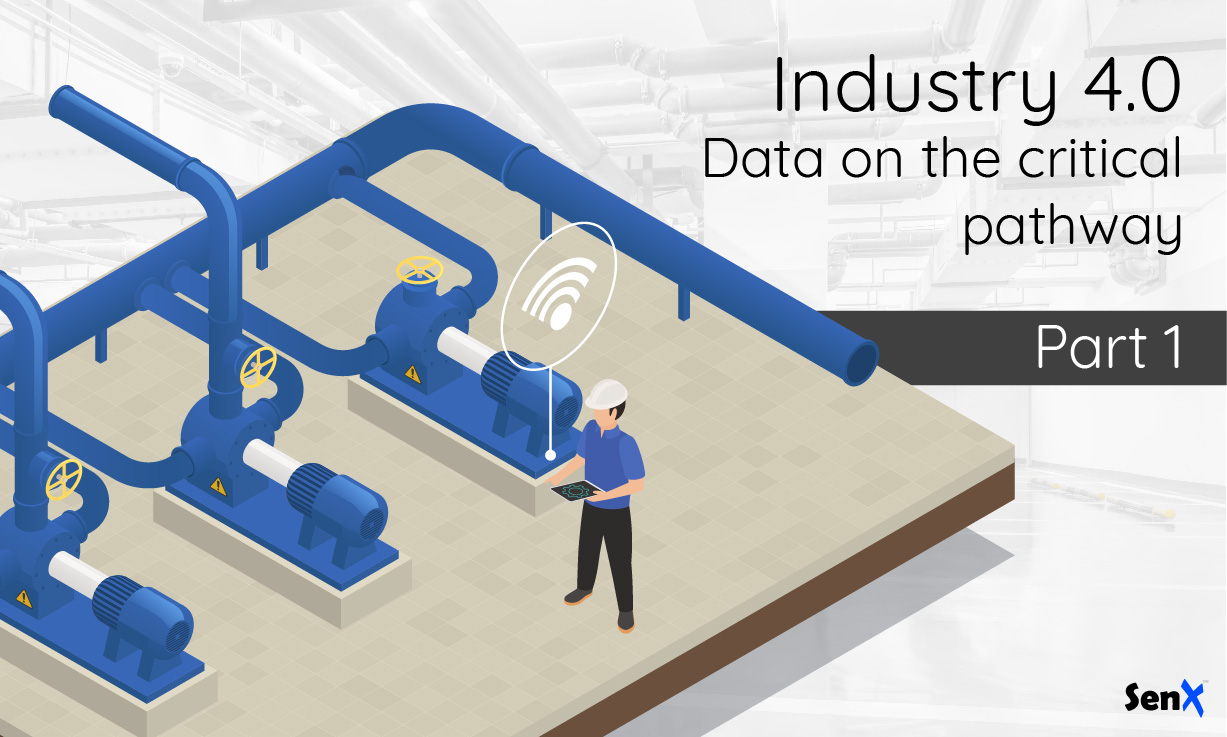
Industry 4.0 results from the digitalization of production tools with ever more sensors and data. Time series opens up new horizons both for the business and for the development of new services.
The transformation of industry, driven by digital technologies, is forcing us to rethink a value chain that is becoming more technically complex. Beyond the manufacturing process, it is profoundly modifying relations with both customers and suppliers. It also highlights the crucial role of data at the crossroads of issues such as productivity, quality, cost control, development of new services, and competition.
This evolution is based on the integration of sensors and measurements at all levels. As a consequence, it emphasizes what the processing of the data thus generated implies in terms of disruption.
This paper is part of a series of articles on how time series revisits the way data are organized and the technologies used for their analysis. After a first paper of general scope, the following papers deal with different sectors, including the industrial sector. |
Vous préférez lire cet article en français ? C'est par ici.
Sensors have always had a special place in the industry. Measurements – with their displays – of voltage or power consumption, pressure and temperature are an integral part of the industrial world. Over the years, measurements have been concentrated on production or operational monitoring stations. Today, sensors are no longer limited to simple measurements of a few variables. They reflect a gradual and continuous digitalization of machines, systems, and technical processes.
The industrial sector is just emerging from a long period of sometimes heavy computerization with the generalization of ERP systems. The widespread use of sensors is paving the way for a transformation towards the Industry of the Future. Better known internationally as "Industry 4.0", the common thread is data, which now has a strategic value.
Several pitfalls can make this journey difficult.
Industry 4.0: a challenge for international competitiveness
The concept of "Industry 4.0" was launched by Germany in 2011. Initially limited to industrial production, it mainly covered the scope of the factory of the future. Today, it generally encompasses everything related to the transformation of industry through the contribution of digital technologies.
For manufacturers, the challenges go beyond the simple technical or technological evolution of their production tools.
They combine two forms of trends that are historically contradictory in industry. On the one hand, the quest for a reduction in production hazards, whether they are due to interruptions in supply or in the logistics chain, or whether they result from the unavailability of production resources. On the other hand, competitive pressure towards ever more personalized products for more demanding customers in terms of services, all in a context that imposes more restrictive rules in terms of energy, environment, safety, etc.
The pillars of the industry 4.0
In 2015, the Boston Consulting Group formalized 9 pillars that define the transition to Industry 4.0. Widely used, this representation puts the major role of data processing and analysis in the foreground. Two other pillars are directly linked to it: the Industrial Internet of Things (IIoT) and simulation with the Digital Twin. We could also add the "Horizontal and vertical systems integration" pillar, which highlights the need to have a technical organization of data that allows such integration.
Sensors – the IIoT pillar – play the role of catalyst in this evolution. Their development conditions the way in which manufacturers will respond to the twofold constraint set out above:
- Reducing hazards: machines and systems are increasingly complex with a strong penetration of electronics and technical software which tend to optimise the overall functioning as well as that of each component by relying on continuous sensor measurements. Just like a car full of electronics, mechanical control is no longer enough. The sensors themselves make it possible to meet the requirements of improved operational quality and to better detect faults. Both internal users and customers want to have better control and avoid being subjected to the vagaries of the operation of complex systems.
- Responding to the challenges of customisation in a more constrained competitive and regulatory context. Everything is measured, both to correctly articulate the interdependencies of systems, to monitor everything that can be monitored and to reduce, as much as possible, the burden and pressure on people.
Most of the other pillars of Industry 4.0 can be conceived as components that can be added gradually. But the more complex one of horizontal and vertical systems integration remains a technological and organizational thorn in the side of transformation.
At least two reasons can be given:
- Systems are based at different levels on a notion of functional and organisational responsibility which results in siloed information systems. Integrated architectures may be attractive in principle, but they are technically difficult to implement and organisationally complex, with financial implications (who pays for what?).
- This verticality in silos implies strong technical constraints on the organisation of data. While it should be easy to cross-reference the different data sources, this work is, on the contrary, tedious and technically difficult due to the heterogeneity of the format and the real meaning of each data source.
In industry, these constraints are all the more marked as the digital perimeter covers two sets that are still too far apart: the company's information systems (or management information systems) on the one hand, and technical information systems on the other.
Find out how time series data helps create digital twins of assets and plays a major role in the use of AI in the Industry 4.0. Read the article |
The separation between business and technical computing
The need for a global operational and financial vision and the constant search for process optimization has led to the widespread use of ERP systems, which, even more than in other sectors, have gradually become established in most industrial companies. With dedicated modules, ERP systems cover procurement, asset management, production management, maintenance management, sales, accounting, and human resources. ERP systems thus cover the whole of IT (Information Technology).
On the side of the machines and technical systems that have to be produced and then operated, we move into another world: that of industrial IT or OT (Operation Technology). The control and command of machines and systems require specific devices to adapt to a wide range of constraints.
In the example of a factory, the whole chain is more complex. It can be represented as follows:
The SCADA
More globally, whether it is the factory itself or machines or systems in production, the link between the world of IT systems and the world of machines and technical systems (OT/Operational Technologies) is made at the level of SCADA (Supervisory Control and Data Acquisition). It is the central part that allows one or more systems, machines or technical devices to be controlled from the information sent back by the latter, from the orders and commands that it may receive from other applications or from business operators who, for this purpose, have a human-machine interface (HMI).
Associated with SCADA, there is increasingly a Data Historian that records local data flows. Analysis tools can be associated with Data Historians. These can be used to answer basic questions about the operating statistics of machines, systems, or any device with a sensor, such as a valve. These can also be fed back, in whole or in part, to a central level.
The SCADA can control several machines and systems. Depending on the case, the link may be direct or may be made to each of them via other decentralized devices (identified in the previous diagram as PLC, DCS, or RTU). In a number of cases, these devices are directly integrated into the machine or system for its operational control and monitoring.
An analogy can be made with the control of a television set in this stack of systems. The box makes the link with the operator and controls the television. The television itself is equipped with its own operating system. The user has one interface to access the box service and another to access the television. There may be an overlap of several functions between the services offered by the box and by the television. |
The link between the SCADAs that control the technical systems and the IT is rarely direct. In general, it takes place via software for managing production, its processes, scheduling, and the operational management of the whole. In the case of a factory, the MES (Manufacturing Execution System) has a special place in the scheduling of tasks and the overall organization of production lines.
In other words, the IT resources of an industrial player organized around its ERP and the world of machines with their control systems and automation have every reason to be far apart.
However, the integration of the IT and OT worlds is unavoidable. Two requirements make it necessary in an increasingly competitive industrial context: the need to respond ever more effectively to operational constraints, on the one hand, and the transformation of customer services, on the other.
The use cases
The next article will focus on the two main use cases of sensor data in the industry. The first use is a natural extension of the raison d'être of sensors in the industry, namely the optimization of system operation. The second is more novel and potentially disruptive for companies: the development of new services for customers.
Follow SenX and Warp 10 on Twitter for future blog posts.
The continuation in the 2nd part.
Discover the different stages of maturity of Industry 4.0 in the video below. (English subtitles available)
Read more
Les TSDB ne sont pas toujours la bonne solution
Introducing FLoWS, a functional language for Time Series Analytics
Warp 10 and the Ethereum blockchain
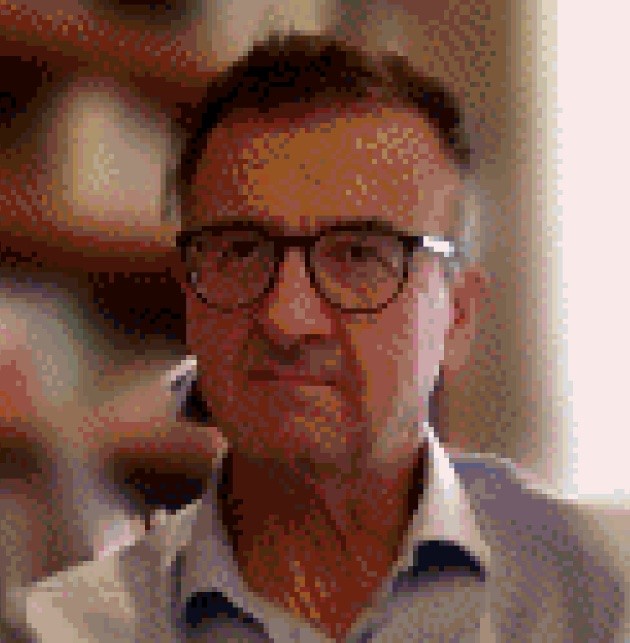
Co-Founder & former CEO of SenX