Les données de capteurs dans l’industrie 4.0 : un changement de référentiel dans l’optimisation et la maintenance des machines et des systèmes, et une source de revenus récurrents avec la création de nouveaux services clients.
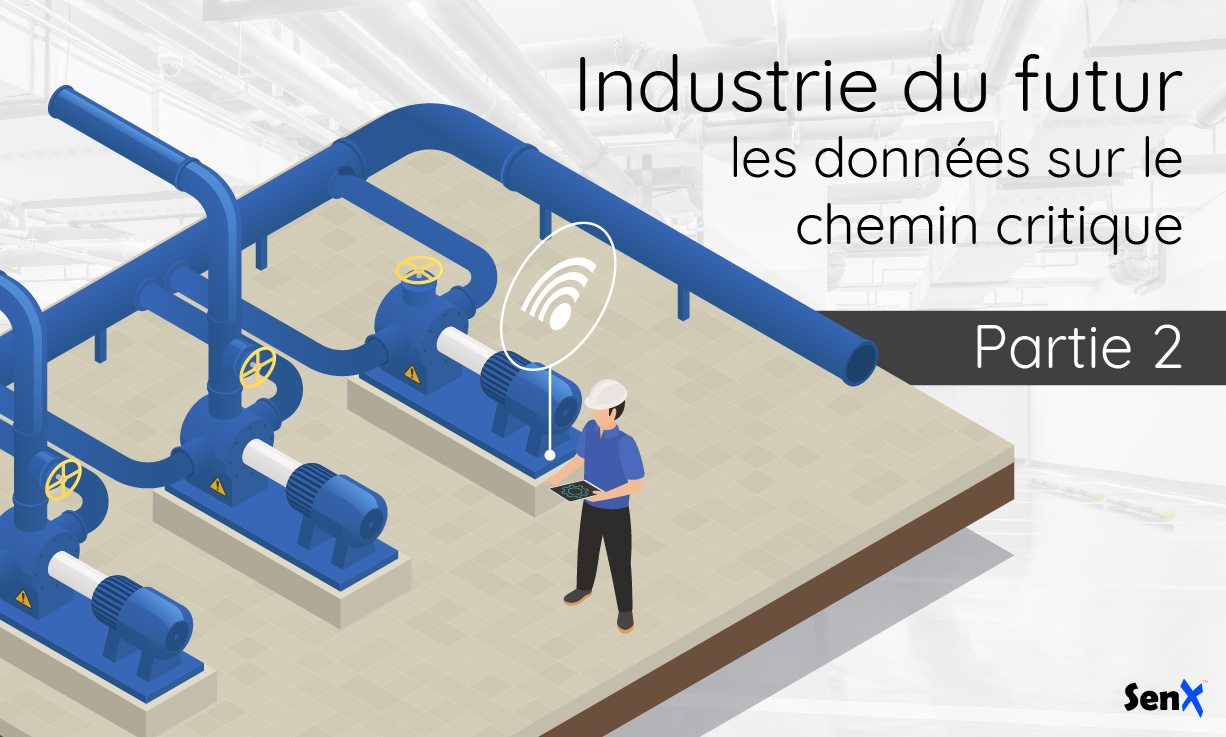
Le présent article constitue la seconde partie d’une série de trois articles sur l’industrie du futur et la manière dont les données vont jouer un rôle majeur dans la transformation des entreprises de ce secteur.
Vous n'avez pas lu la première partie ? C'est par ici.
Prefer to read this article in English? It's right here.
Les données de capteurs au service de l’optimisation du fonctionnement des systèmes
L’exigence opérationnelle implique un fonctionnement des systèmes qui doit tendre vers le zéro défaut et une disponibilité totale.
L’imbrication et les interdépendances entre les systèmes sont telles que l’arrêt de l’un d’entre eux est susceptible d'entraîner des effets en chaîne, qui peuvent avoir, très rapidement, de lourdes conséquences financières. Cet état de fait confère un caractère critique à la maintenance avec, en contrepartie, un coût demeurant un sujet constant de préoccupation pour les entreprises. Le rapport entre le total des coûts de maintenance et de réparation avec le montant des investissements correspondants (ratio souvent utilisé), est en moyenne de 7 % du montant initial des investissements, même s’il peut fortement varier d’une industrie à l’autre.
Il existe trois modèles de maintenance classiquement retenus par les entreprises :
- La maintenance réactive. Elle limite les coûts récurrents et peut être adaptée à un équipement dont la probabilité de panne est considérée comme très faible. Ainsi la contrepartie de la limitation des coûts récurrents est une prise de risque dont les conséquences peuvent être lourdes, le cas échéant.
- La maintenance conditionnelle. Elle s’appuie sur un suivi en continu du comportement d’un système en vue de déclencher des actions de maintenance lorsque cela paraît le plus opportun. La difficulté consiste alors à gérer correctement les critères de prise de décision d’arrêt d’un équipement. Trop souvent, la pression opérationnelle est telle que, dans les faits, la maintenance conditionnelle glisse vers une maintenance réactive.
- Et la maintenance préventive. Elle implique à la fois d’immobiliser les équipements, de disposer d’un stock de composants de rechange et d’équipes dédiées. Cette dernière est notamment pratiquée dans les secteurs très fortement réglementés, comme l’aéronautique ou le nucléaire par exemple.
Les deux premières formes de maintenance s’appuient sur des mesures issues de capteurs. Elles sont exploitées en temps réel au travers de seuils tels que : valeur normale, valeur à surveiller, valeur anormale (alarme), valeur dangereuse (alarme critique). Quant à la maintenance préventive souvent perçue comme coûteuse, elle est basée sur une gestion d’actifs (ou Assets Management). Elle est, le plus souvent, complétée par une maintenance conditionnelle.
La Maintenance Analytique comme voie intermédiaire vers l'industrie du futur
L’exploitation analytique de l’historique des mesures ouvre une voie intermédiaire, avec, grâce aux capteurs qui se multiplient, une compréhension possiblement exhaustive du fonctionnement d’un équipement dans ses moindres détails. Il faut disposer de capteurs pertinents et performants qui transmettent un nombre suffisamment de mesures. Il faut ensuite disposer d’outils techniques performants qui vont être capables de stocker des historiques suffisamment profonds et d’analyser les données, le cas échéant en grandes quantités, en régime de production.
Cette voie intermédiaire est celle de la Maintenance Analytique, basée sur l'analyse de séries temporelles de données avec une préférence au passage pour une terminologie plus large que celle de maintenance prédictive. La Maintenance Analytics couvre quatre types d’analyses : l’analyse descriptive, le diagnostic, l’analyse prédictive et l’analyse prescriptive.
Ses atouts
En termes de coûts directs, elle se situe entre la maintenance conditionnelle et la maintenance préventive.
Mais les coûts directs ne sont pas les seuls à prendre en compte, comme l’illustre les deux planches suivantes :
La première de ces planches montre l’impact financier de l’immobilisation d’un équipement du fait d’une maintenance préventive planifiée ou sous l’effet d’une panne.
Dans les deux cas, la maintenance analytique permet de diminuer l’impact financier. Deloitte estime ainsi que la seule Maintenance Prédictive peut réduire le temps consacré à la maintenance de 20 à 50 % tout en augmentant le temps de disponibilité des équipements de 10 à 20 %. McKinsey propose des chiffres proches : baisse des coûts de maintenance de 20 à 30 %, diminution de l’indisponibilité de 20 à 50 %. Il met également l’accent sur les résistances organisationnelles.
La maintenance analytique permet aussi de réduire les effets négatifs indirects que peut avoir l’arrêt d’un équipement en termes de désorganisation potentielle de l’approvisionnement et des ventes. Une machine ou un système est en effet intégré dans une chaîne qui, du fait de la panne d’un seul maillon, peut se trouver totalement immobilisée.
Les répercussions peuvent alors avoir de lourdes conséquences en amont dès lors qu’il s’agit de suspendre les approvisionnements. Mais également en aval, avec des suspensions des livraisons clients et leurs éventuelles conséquences commerciales (pénalités, baisse de confiance des clients, perte de nouveaux contrats). Les coûts indirects qui en découlent sont probablement les plus importants et sont aussi les plus difficiles à estimer.
De fait, le bénéfice d’une maintenance analytique ne fait guère de doute sur le bénéfice pour l’entreprise en termes de coûts de la maintenance.
Encore faut-il disposer d'outils perforants et industrialisables qui vont être en mesure de traiter les données tout en interagissant avec le système d'information de l'entreprise et donc avec les différents modules de l'ERP tel que nous avons pu le voir dans le premier article. C'est bien l'ambition de Warp 10 dans des environnements les plus variés avec des données de capteurs potentiellement nombreux, variés, avec chacun des comportements différents.
Les données de capteurs pour transformer la relation client
La transformation la plus importante est complémentaire à celle qui touche la maintenance. Elle est liée aux nouveaux usages qui sont progressivement fait de la donnée technique. Alors que celle-ci n’avait qu’une valeur opérationnelle liée au fonctionnement des équipements, machines et autres systèmes, elle devient progressivement l’enjeu de la transformation de la relation entre un fournisseur et son client.
Cette orientation n’est pas nouvelle sur des sujets comme l’énergie ou la mobilité. La donnée y était utilisée à l'origine pour assurer et optimiser le fonctionnement technique des réseaux, des bus, des voitures. Elle intéresse désormais l’utilisateur tout comme les nombreux prestataires qui peuvent lui proposer de nouveaux services. De ce fait, la segmentation du marché s’est complexifiée avec la nécessité, pour chaque acteur – qu’il veuille conserver son leadership ou souhaite se positionner en nouvel entrant sur la chaîne de valeur – le besoin impérieux de contrôler les données. Et avant tout, celles qu’il génère par ses propres systèmes et équipements.
L'apparition de nouveaux services
Même si le cadre et les modalités diffèrent, l’industrie suit la même voie, sous des formes variables selon les secteurs. En ligne de mire de cette évolution : une transformation profonde du métier auquel tout industriel pourrait être confronté si ce n’est déjà le cas : la transformation d’un produit industriel en service.
Nous illustrons ici par un exemple ci-dessous.
Someflu est un fabricant de pompes industrielles, de pompes centrifuges anticorrosives notamment, destinées à véhiculer divers fluides corrosifs ou abrasifs.
La maintenance de ces pompes est très importante du fait des produits en jeu et des contraintes opérationnelles ou de sécurité pesant sur les industriels utilisateurs. Dans le même temps, le fabricant exerce dans un contexte concurrentiel international où le prix de vente joue un rôle primordial.
Alexandre Lacour, le directeur de Someflu, a constaté que le traitement des données de capteurs lui offrait l’opportunité de changer de modèle. En choisissant de systématiser leur usage, il se donne, en autres exemples, la possibilité à terme :
- d’effectuer des tests exhaustifs en sortie de production de manière systématique ;
- de disposer d’une vision en temps réel de l’ensemble du parc des équipements par clients ;
- de comparer les systèmes et de détecter le fonctionnement discordant d’un équipement ;
- d’analyser le vieillissement de chaque équipement ou famille d’équipements ;
- de prédire des défaillances potentielles ;
- de programmer les opérations de maintenance de l’état réel des pièces d’un équipement.
Il peut, aussi et surtout, faire bénéficier son client de cette vision exhaustive de ses équipements. De nouveaux services rendus disponibles via Internet ou directement sur mobile peuvent être développés à cet effet. Le tout, avec des liens avec son propre système d’information. Ces services qui peuvent être facturés, constituent alors une nouvelle source de revenus pour l’industriel ; ils sont en outre récurrents, ce qui est de nature à modifier en profondeur la nature de la relation avec son client.
Ainsi, Someflu acquiert une capacité à faire évoluer le mode de tarification de ses équipements en jouant sur l’équilibre entre le prix de vente et celui du service. In fine, le prix de vente pourra être, le cas échéant, nul puisque intégré dans un coût de service global.
SenX accompagne Someflu dans cette transformation avec une récupération des données de capteurs et, grâce à Warp 10, une analyse avancée qui lui permet de viser un changement de son modèle économique. Son dirigeant Alexandre Lacour, est désormais impliqué dans la Filière Industrie du Futur avec une vision qui est précisément celle qui est mise en avant tout au long de ce présent article. Cette vision est notamment très bien décrite dans une vidéo en ligne qui est particulièrement éclairante.
Les SCADAs et les jumeaux numériques
Le dernier article de cette série abordera la problématique des SCADAs et l’un des sujets les plus en vogues du moment sur la thématique de l’industrie du futur, à savoir le jumeau numérique.
Suivez SenX et Warp 10 sur Twitter pour ne pas manquer le dernier article de la série sur l'industrie du futur.
Découvrez les différentes étapes de maturité de l'industrie du futur dans la vidéo ci-dessous.
Read more
When do you need a Time Series DataBase?
Thrift and Protocol Buffers support in WarpScript
Warp 10 for IoT: GDPR compliant before GDPR even existed
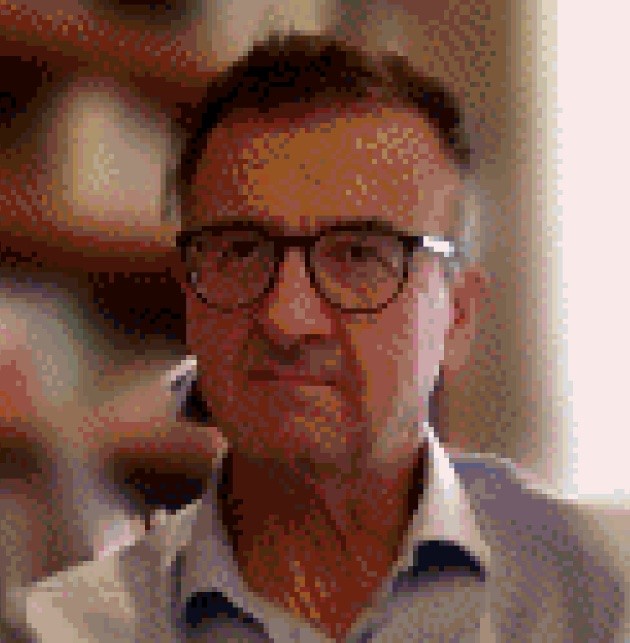
Co-Founder & former CEO of SenX